What is Injection Foam?
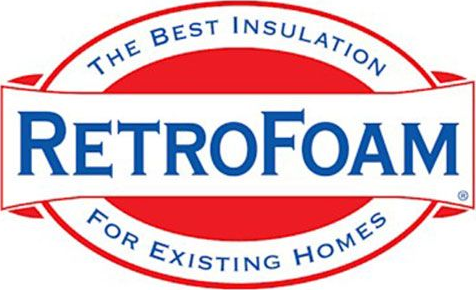
RetroFoam "the product" by name alone is injection foam.
It looks and acts much like white shaving cream. It is primarily used to retro-insulate an existing home's enclosed wall cavities. While it is most popular for exterior walls, it is becoming more common to use to dampen interior and exterior walls from airborne noise. We can often use RetroFoam injection foam in sloped or vaulted ceilings or flat garage ceilings below bonus rooms.
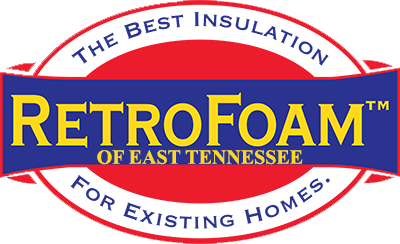
RetroFoam of East TN LLC is the name of our locally owned small business.
We belong to a larger network of independent privately owned dealers that make up a family of professional foam insulation contractors. This means you will be handled by people who care deeply about their reputation, and not some large franchise that has unclear ownership. Our owner and manager are local…reachable, and often seen on the job site checking on the accuracy of the installation. We are always here after the sale to help.
Superior Insulation Solutions With Injection Foam
Injection foam is the latest innovation in insulation. As a new-generation option, it has a tri-polymer mix of resin, water, air, and a foaming agent. It's non-toxic and odor-free. When mixed on-site, it creates a soft, malleable foam like shaving cream. Then, it can be injected into most common wall cavities. Our installers make every effort to map out the stud cavities so we know exactly where injection foam will and will not be applied. In rare cases, there may be a small stud or framing cavity that is inaccessible or too risky to foam. We use a common-sense approach for every injection foam installation! injection foam installations include several standardized and time-proven testing methods to ensure a proper product mix for every project. The foam fills the gaps in the cavity, providing superior insulation coverage and saving you money while enhancing your comfort.
Insulation is designed to protect your home from the elements. It doesn't just keep your home comfortable, but it also helps control your energy costs by keeping air from leaking through the walls, ceilings, and floors. At RetroFoam of East Tennessee, we get this done with a unique spray foam formula from the insulation experts at injection foam.
Serving Knox County, TN and surrounding areas, we bring over 18 years of experience to every project. Our specialized team raised right here in Knoxville, TN, treats every house like it's our grandma's. With a commitment to quality and customer satisfaction, we provide:
- Raw-injection foam insulation
- Attic fiberglass insulation
- Wall insulation
- Spray insulation
- Pole barn insulation
- Metal building insulation
- Crawlspace insulation
- Complete home weatherization
- Home insulation
Call or text us today to learn more about our services and how we can help improve your home's energy efficiency. We have injection foam options with R16 and R18 values. Get a free consultation today!
Benefits of Choosing RetroFoam of East Tennessee
At RetroFoam of East Tennessee, our team is dedicated to providing exceptional service and ensuring your home is well-insulated. Here are some benefits of working with us:
- Small, local business
- Free consultations over the phone
- Affiliated with GES Custom Remodel
- TVA EnergyRight contractor
- Preferred contractor with Owens Corning
- Andersen-certified contractor
- Serving you since 2006
- All work guaranteed
- Liability insurance
- Employees get continuing education
Get in touch with us today to experience the benefits of injection foam insulation for yourself.
Contact Us for Injection Foam
Don't wait to improve your home's insulation. Call or text us at RetroFoam of East Tennessee. Our team is here to answer your questions and provide the solutions you need.
Share On: